Manufacturing

The people behind our products. Family first. Not only in our own lives, and the families who buy our products but also the people and families who make our products. When Bumbleride was born in 2004, we discovered a factory in Taiwan that was a family-owned and run, assembly factory with ethical working conditions, fair pay and more recently a 5-day work week with no overtime (vs. 6 days elsewhere). We knew this was a match. Better conditions can mean higher costs, but we believe there is a much higher human value and we know personally that the families of those that work at our factory appreciate these things. Our factory works with 50+ sub-contractors in Taiwan who are all small businesses, often family owned as well. This fits right in with our business philosophy, which is built on strong relationships rather than seeking the lowest cost option. We’re very proud to still be working with the same factory we started with in 2004 and appreciate our unique partnership we’ve built together. When our founder visits Taiwan, it’s work and play – complete with hiking, organic farming and sharing meals together.
We Are Bumbleride
Quality Matters. Our small batch production approach means craftsmanship that keeps the quality consistent, while only producing what we forecast out to reduce excess waste. Being in tune with our factory and every step of the production process, allows us to be part of the progression from concept to completion, overseeing every small detail. The ability to talk to the factory owner at the drop of the hat goes above and beyond the communication path we imagine in the mega factories.
Doing the right thing. Our focus on choosing materials with the least environmental impact, yet also integrating durability and performance, can happen seamlessly by working together closely and sharing the same vision. We seek to keep our products as close to us as possible to keep the quality consistent, but to also be aware of everything happening behind the scenes. This means paying attention to details, for example if we work hard to source recycled materials, but then poorly manage production quantity or waste, then the environmental benefit is lost. Our factory shares our vision and produces very little waste and reuses or re-purposes almost everything. Being conscious in all aspects of the manufacturing process is vital because it can be a very dirty business. Larger factories may be able to afford expensive certifications and market themselves as such. We highly value the criteria and importance of certifications that promote worker safety, fair policies and environmental protection. However, from our experience knowing who makes your products and their processes is even more important. Just like we would rather buy from the local organic farmer than a mega organic food brand. Doing the right thing is not always obvious, but is rewarding to know that we are trying our best to do our part.
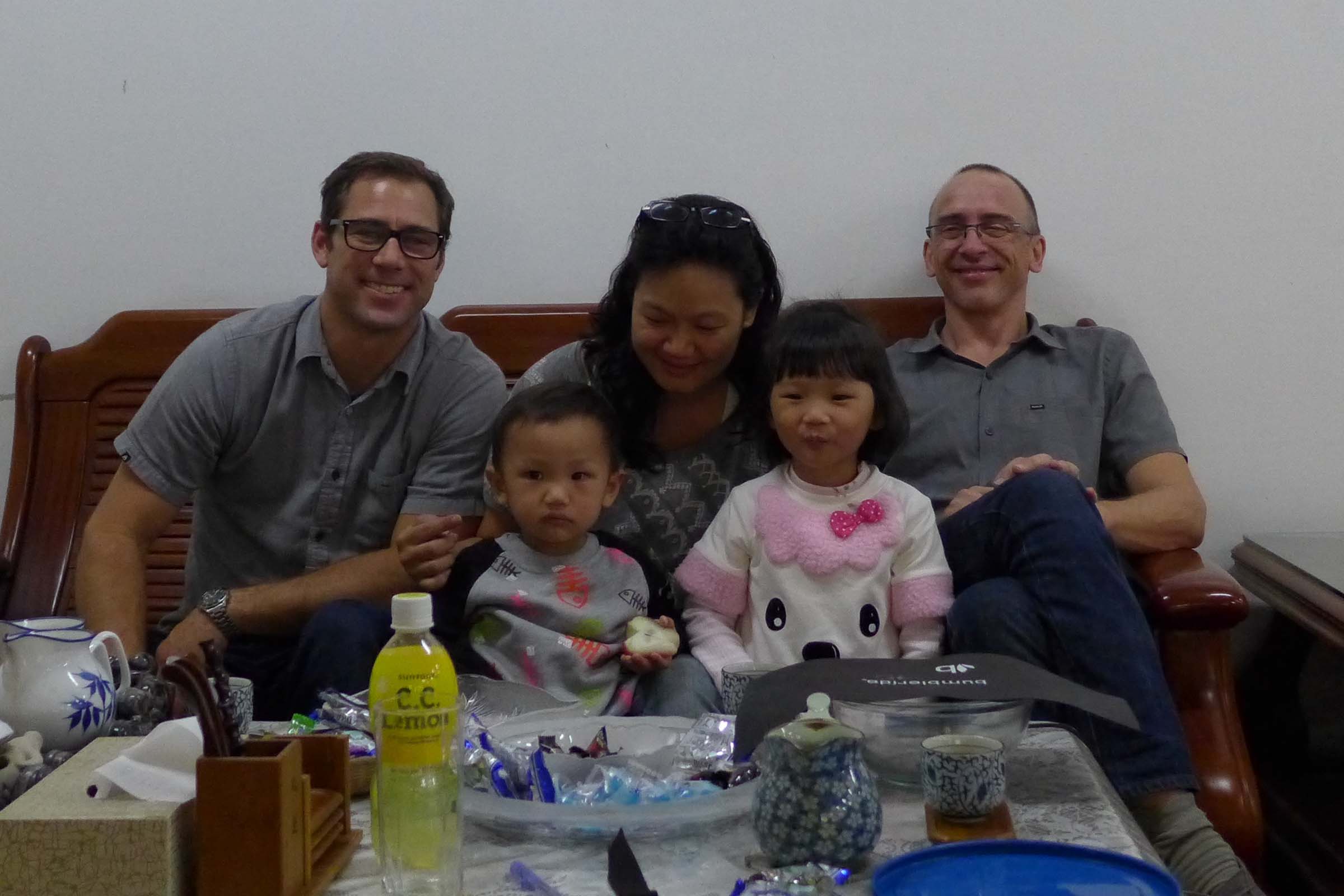